
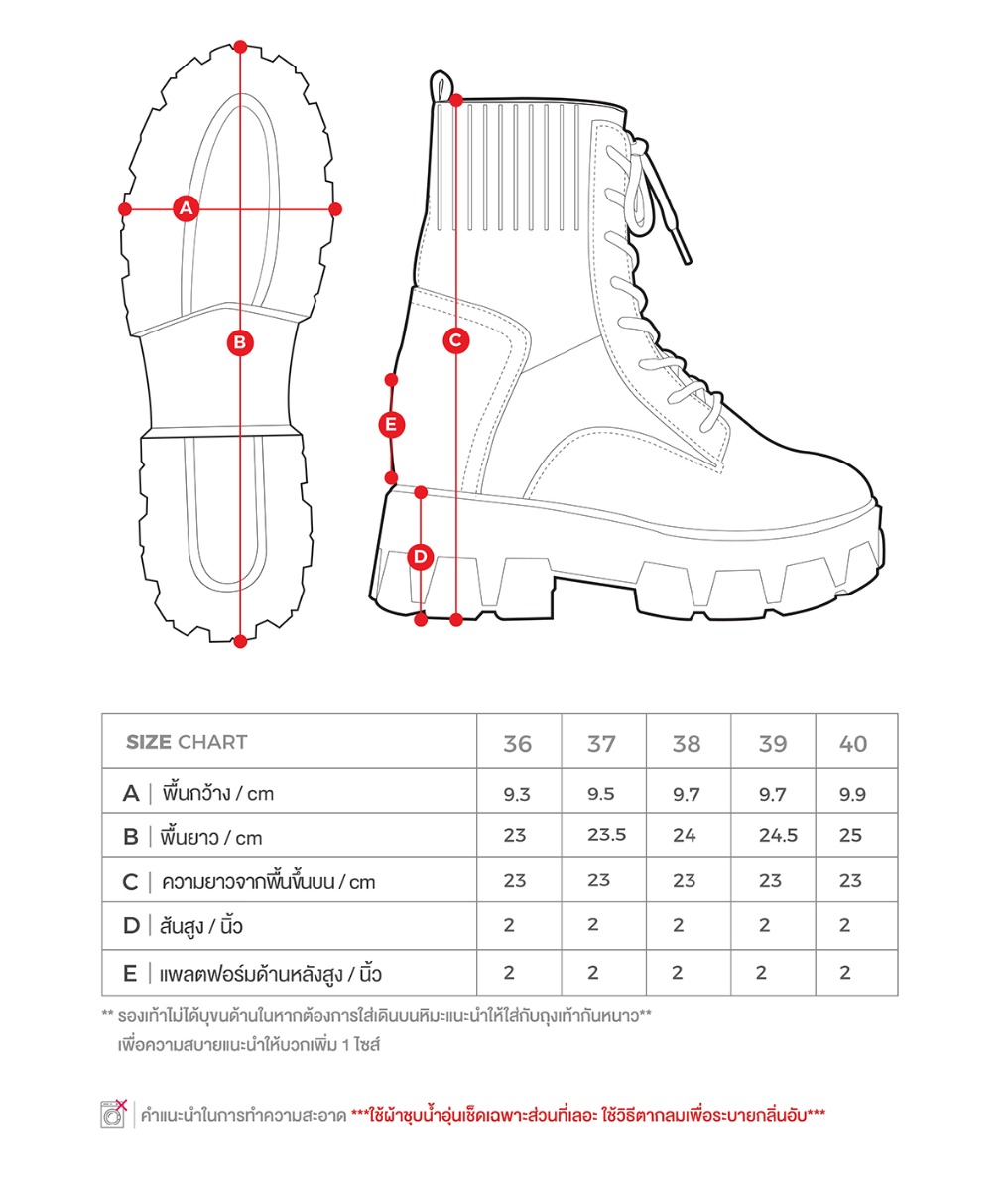
Although width-restricted in the hold by the aft vessel crane, a stowage plan was agreed upon.ĭuring discussions between Bertling Logistics and the Harbour Master, safe passage under the Transporter Bridge at a certain tide height was confirmed as feasible and suitable draught and tidal curves were confirmed to be available during neap tides on six days per calendar month.Īdditional OOG cargo had been added to the scope of Bertling, which include the transportation to their Middlesbrough base and stowage of general cargo into 20 x SOC’s as well as loading 5 x items of additional OOG cargo.

The selected vessel type had an open dock hull arrangement. The two known operational limitations for the location were available draught alongside the yard and a headroom restriction downstream in the form of the historic Tees Transporter Bridge.Īddressing these two issues to pass under the bridge, the Tower had to be stowed inside the hull of the HL vessel, and to mitigate the draught issue, the Tower would need to be “lightered” by barge across the river alongside the HL vessel where much deeper draught was available at the Port of Middlesbrough.īertling Logistics advised the best method of jacking the Tower up to SPMT height, a challenging task for a structure of almost 1,000Te and over 40m high.Ĥ x 500Te capacity perpetual climbing jacks were proposed, and Bertling Logistics provided design assistance to allow the retrofitting of the required jacking lugs that would ultimately allow the insertion of the SPMT’s beneath the Tower to allow it to be site moved to the quay edge. The Tower was located at Port Clarence on the river Tees in Middlesbrough, near the home of Bertling's Heavy-Lift and Engineering Team. To find the best technical and commercial solution, Bertling Logistics performed a study for all possible shipment modes, including heavy lift vessels, gearless vessels with shore/floating cranes, and ro-ro vessels.
